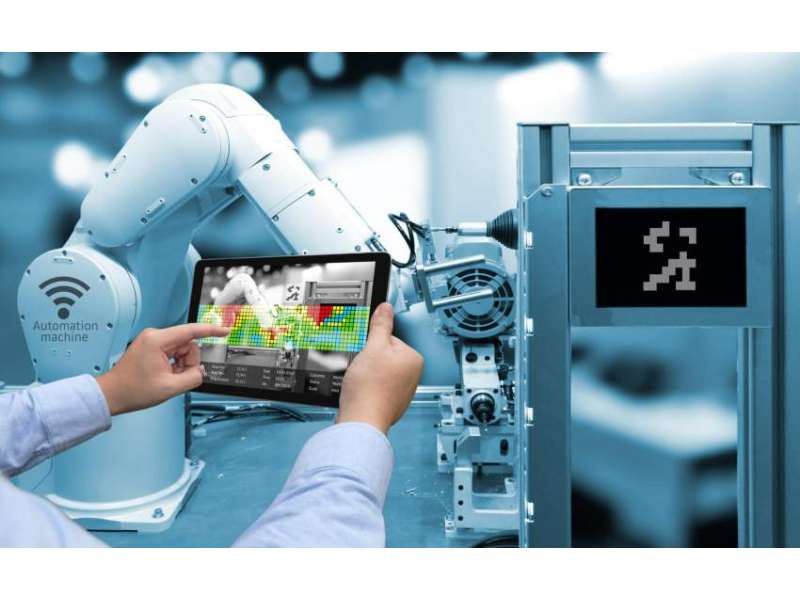
#Industrie 4.0 : Le #JumeauNumérique donne vie à l’#Industrie 4.0
Couplant simulation et données, le jumeau numérique colle au plus près du système réel qu’il modélise.
L’industrie l’utilise pour surveiller, maintenir et optimiser ses machines et ses produits.
Classé parmi les dix grandes tendances technologiques stratégiques selon Gartner, le jumeau numérique s’installe progressivement dans le paysage industriel mondial. Si, aujourd’hui, peu d’entreprises exploitent encore cette technologie en production, les deux tiers de celles ayant une stratégie dans l’internet des objets (IoT) devraient la mettre en place d’ici à 2022, selon le cabinet de conseil.
Formulé pour la première fois en 2002 par le chercheur Michael Grieves (université du Michigan), le concept de jumeau numérique ne cesse d’évoluer au fil du temps et des objectifs des entreprises. Sous une forme assez générique, Gartner le définit comme le modèle numérique d’un process ou d’un objet réel, rendu dynamique par les données issues de ce même process ou objet.
Il ne s’agit donc pas d’une simple copie virtuelle d’une pièce ou d’un process génériques, « mais d’un véritable jumeau individuel conçu pour suivre en temps réel les transformations de l’objet ou du process spécifique auquel il est attaché, de sa conception jusqu’à sa destruction », insiste Éric Martin, directeur de l’École nationale supérieure d’ingénieurs de Bretagne Sud (Ensibs), à Lorient, où une chaire Jumeau numérique vient d’être créée.
#Modèles alimentés en continu par des données
Quelles que soient ses spécificités, le jumeau numérique s’appuie sur un ensemble de modèles physiques utilisés pour réaliser des simulations. Soit résoudre numériquement des équations issues de la physique afin de prédire la façon dont le système réel se comporte. La spécificité du jumeau numérique réside dans le fait que ces modèles vont être alimentés en continu par des données collectées via des capteurs disposés sur le système réel, ou issues de la dernière inspection en date.
Ainsi, contrairement à la simulation classique, les modèles du jumeau numérique peuvent tourner sans cesse afin de pouvoir fournir à chaque instant des informations sur l’état actuel de fonctionnement du système réel auquel il est relié. Mais aussi des prédictions en temps réel sur ce qui, au regard de son fonctionnement actuel, va se produire dans les secondes, les minutes, les heures, ou les semaines à venir [lire l’encadré ci-dessous].
De quoi permettre une surveillance accrue ou d’anticiper d’éventuelles pannes. « Pour une éolienne, en fonction de la vitesse de rotation du moteur ou de la pression exercée par le vent, on pourra prévoir à chaque instant l’usure des matériaux de chaque pale en faisant tourner des modèles de fatigue de ces pales alimentés par les dernières données collectées. Aux premiers signes d’usure, l’information est remontée à l’opérateur qui arrête l’éolienne afin d’effectuer des travaux de maintenance préventive », explique Sébastien Kawka, responsable d’applications chez le fournisseur de logiciels Comsol.
#Obtenir les meilleurs leviers d’optimisation
« Quand l’ensemble d’un parc est répliqué et son évolution simulée, on peut prédire à quel moment et comment précisément vous avez intérêt à procéder à chaque réparation pour minimiser l’impact sur votre production et maximiser son efficacité. Il s’agit, par simulation, de visualiser ce qu’il se passe si je modifie tel ou tel paramètre et, par comparaison entre les différents scénarios, d’obtenir les meilleurs leviers d’optimisation et le meilleur plan d’action », détaille Michel Morvan, le président de la start-up lyonnaise Cosmo Tech, qui a déployé sa solution de jumeaux numériques chez Renault.
Pour fournir des prédictions compatibles avec des prises de décision rapides, de l’ordre d’une fraction de seconde pour des voitures autonomes ou de la journée pour une éolienne, il a fallu augmenter la rapidité des simulations. Certains éditeurs ont donc retravaillé le code de leurs logiciels de simulation.
« L’efficacité du calcul dépend en grande partie des algorithmes. En douze ans de recherches, nous sommes parvenus à revisiter ces derniers pour accélérer la simulation. Nos algorithmes sont capables d’exécuter des milliers de simulations en moins d’une heure, nous permettant de sortir en vingt-quatre heures des rapports qui prenaient auparavant entre quatre à six mois. Nous restons cependant sur des physiques relativement simples », explique Thomas Leurent, le CEO de la start-up vaudoise Akselos, qui développe un logiciel dédié à la maintenance d’infrastructures techniques. « D’autres ont préféré simplifier leurs modèles en réduisant les nombreux paramètres à quelques paramètres effectifs afin qu’ils puissent tourner plus vite », indique Sébastien Kawka.
#Anticiper tous les scénarios grâce à l’IA
D’autres encore utilisent des abaques numériques. Soit un tableau regroupant une large palette de calculs numériques pré-effectués afin d’opérer rapidement. Au regard des paramètres d’entrée actuels, ce système permet de trouver au sein du tableau des cas de calculs similaires déjà effectués dans le passé et d’interpoler directement un résultat.
Enfin, certains intègrent des outils d’intelligence artificielle (IA) à leurs solutions. Dans ce cas, les modèles auront préalablement fait l’objet d’un grand nombre de simulations permettant d’anticiper tous les scénarios de comportements possibles en cas d’incident (panne, collision, fatigue…). Et « c’est sur ces données simulées auxquelles s’ajoutent les données observées dans le passé que des outils d’IA (deep learning, réseaux de neurones…) s’entraîneront pour formuler des prédictions rapides selon les conditions d’exploitation des équipements et détecter la moindre anomalie », précise Elie Hachem, professeur à Mines ParisTech et responsable du projet Minds, qui a l’ambition de « créer une plate-forme numérique de R & D couplant le monde de la simulation numérique et l’IA, afin d’offrir des réponses précises et complètes aux industriels ».
Très diverses, les solutions de jumeaux numériques proposées sont multi-modèles et multi-échelles. Il peut s’agir de simuler le fonctionnement d’un seul élément, d’un sous-système ou d’un système complet. « On peut aller très loin et réaliser les jumeaux numériques d’entreprise. Le jumeau comprendra alors des composants très hétérogènes : les machines, mais aussi le processus de production, les ressources humaines et même les contraintes financières… », explique Michel Morvan (Cosmo Tech).
#Deuxième vague avec l’aéronautique et le Défense
À Singapour, la solution 3DExperience de Dassault Systèmes doit permettre, en incluant les données de construction et de gestion des bâtiments, ainsi que des réseaux de transport et d’énergie de la ville, de superviser la cité. Longtemps réservée au domaine de l’aérospatial, la technologie séduit aujourd’hui un nombre croissant d’industriels issus de secteurs divers et soucieux de suivre des systèmes complexes, aux enjeux importants.
« Nous avons lancé notre plate-forme Twin Builder en mai 2018 et nous comptons aujourd’hui 500 clients dans le monde, souligne Éric Bantegnie, le président d’Ansys. La demande est venue de l’industrie lourde et des secteurs de l’énergie. Une deuxième vague arrive désormais, issue des secteurs de l’aéronautique ou de la défense. Avec le jumeau numérique, nous nous assurons par exemple du bon fonctionnement des trains d’atterrissage des drones, afin d’éviter qu’ils ne cassent. »
Le secteur des véhicules électriques fait également figure de relais de croissance. Ansys a ainsi conclu, fin 2019, un partenariat avec Volkswagen afin de valider l’ensemble des composants des engins de la marque (batteries, logiciel de contrôle…).
#Le temps réel, une mesure variable
« La notion de temps réel peut recouvrir différentes échelles. On devrait parler de quasi-temps réel. Pour une éolienne, les pannes ne surviennent pas en quelques secondes, mais plutôt pendant plusieurs jours. Les données chargées d’alimenter le jumeau numérique peuvent donc être relevées une fois par jour en moyenne. Au contraire, certains processus comme les turbines à gaz des avions exigent qu’on surveille leur fonctionnement chaque seconde », souligne Sébastien Kawka, le responsable d’applications chez le fournisseur de logiciels Comsol. Aussi, les modèles mis en jeu vont-ils se révéler très différents. Dans le premier cas, on peut se permettre de simuler des modèles complexes qui pourront prendre des heures à tourner. Dans le second cas, il faudra des modèles numériques simplifiés de façon à pouvoir interagir rapidement avec le système physique. »
#Traiter les données au plus près de leur source
« Pour autant, déployer des jumeaux numériques en très grande quantité exige des capacités d’hébergement de ces applications et de pouvoir gérer et administrer correctement de grands volumes de données », note le dirigeant. Comptant déjà quelques dizaines de milliers de jumeaux numériques en fonctionnement, Ansys vient de s’allier à Microsoft, dont la solution Microsoft Azure digital twins permet de créer des modèles complets d’environnements physiques compatibles avec les solutions d’edge computing, qui permettent de traiter les données au plus près de leur source.
« Aujourd’hui, nos jumeaux numériques tournent de manière externe dans des centres de calcul, mais on pourrait imaginer qu’ils soient embarqués dans les systèmes afin que ceux-ci s’auto-surveillent. En cas de décisions critiques à prendre, on éviterait ainsi le temps de latence nécessaire pour envoyer et ramener les données jusqu’aux centres de calcul. Et, en conservant ces données en un même endroit, on en améliorerait la sécurité », affirme Éric Bantegnie.
#Réalité virtuelle et augmentée, les interfaces du futur
Au travers du jumeau numérique, nombre d’informations sur l’état de vie d’un système sont diffusées aux différents utilisateurs. Aujourd’hui, la visualisation des résultats des simulations s’effectue le plus souvent sur un tableau de bord, en 3D. Il est ainsi déjà possible de montrer à un opérateur ce qu’il se passe à l’intérieur de l’objet qu’il maintient. « Mais des solutions liées à la réalité virtuelle ou à la réalité augmentée apparaissent pour démocratiser et rendre plus intelligibles des informations complexes issues du jumeau numérique, explique Olivier Sappin, le directeur général de la marque Catia (Dassault Systèmes). Muni d’un casque de réalité virtuelle, je peux obtenir la représentation complète de l’habitacle d’un véhicule et visualiser les flux d’air qui y circulent. Cela peut aider à mieux appréhender et construire le système de climatisation d’une voiture afin de la rendre plus confortable. » « Pour une interaction plus directe entre l’homme et le jumeau, les futures interfaces devront nous permettre d’utiliser tous nos sens. Que ce soit la vue, le toucher ou même l’odorat. Mais cela impliquera des questions d’ordre psychologique, cognitif et ergonomique », souligne de son côté Francisco Chinesta, enseignant-chercheur CNRS, spécialiste en simulation avancée.
#Améliorer l’interopérabilité
Le partenariat doit également améliorer l’interopérabilité, afin de permettre à chaque jumeau numérique d’une machine ou d’un système de communiquer avec ses homologues. Il s’agit de lancer le développement d’un langage commun de définition des jumeaux. Ainsi, les différents industriels qui produisent les multiples équipements d’une installation (voiture, usine…) pourront exprimer ces modèles de données en un langage accessible à tous, facilitant la tâche des intégrateurs.
Enfin, le dernier défi consisterait à pouvoir expliquer les prédictions produites par l’IA. « Si les modèles physiques sur lesquels repose la simulation classique sont déjà certifiés, nous avons aujourd’hui de nouveaux protagonistes : les données collectées et l’IA, souligne Francisco Chinesta, enseignant-chercheur CNRS, spécialiste en simulation avancée. Il faudra donc pouvoir comprendre comment une machine est capable d’apprendre afin d’expliquer les décisions prises par l’IA et pouvoir certifier ce qu’elle fait. »
https://www.usinenouvelle.com/article/le-jumeau-numerique-donne-vie-a-l-industrie-4-0.N953871